Shaping the Next Generation of Magnets: From Atoms to Applications
Permanent magnets are essential to modern technology, from electric vehicles to wind turbines. But producing them sustainably and without rare earth elements remains a major challenge. In his PhD project at Aarhus University, Priyank Shyam explored how to design and optimize ferrite-based magnets that are both effective and rare-earth-free. His work combines synthesis, structural characterization, property measurements, and performance optimization which are all key pillars of modern materials science.
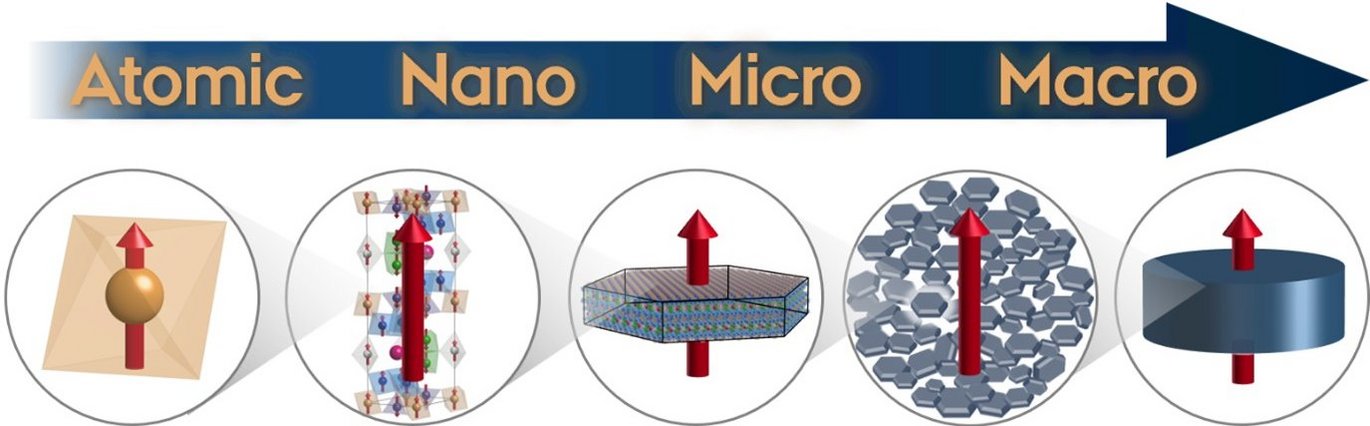
A Search for Better Magnets Without Rare Earths
From turbines that harness wind energy to motors that power electric vehicles, permanent magnets are critical components of modern technologies. Conventional permanent magnets often rely on rare earth elements, which are expensive, geopolitically sensitive and environmentally damaging to extract. Ferrite-based magnets offer a more sustainable alternative, especially when designed as exchange-spring nanocomposites.
These composites combine two magnetic phases: a “hard” phase that holds onto its internal magnetism, and a “soft” phase that delivers strong magnetization. When mixed at the nanoscale, the hard and soft phases can “spring” into a cooperative magnetic behavior – enhancing performance beyond the capability of each individual phase. In theory, this could create strong magnets using only earth-abundant elements like iron and oxygen, without depending on critical rare-earth elements. But the path to a high‑performing exchange-spring ferrite magnet is not straightforward.
Learning from Failure and Finding New Methods
A key initial finding was that sol-gel synthesis, a widely used chemical method, caused unexpected degradation of the hard magnetic phase, thus undermining the exchange‑spring effect and weakening the overall magnetic performance. This early challenge provided a valuable insight: a good magnet depends not only on which phases are present, but also on how they are formed, aligned, and structured. By identifying such pitfalls, he was later able to design better synthesis strategies that improved coupling between the soft and hard phases.
Building a Better Magnet: Three Key Factors
To improve performance, Priyank’s later work changed the approach. Instead of sol-gel methods, he explored alternative bottom-up synthesis routes, including solvothermal and co-precipitation methods. Like any good recipe, making a high-performance permanent magnet requires precise control over what goes in and how it is all put together. Here, the focus was on getting three things “right”: getting “the right atoms” together to form nanoparticles with “the right sizes” which would, in turn, be packed with “the right alignment” in the final magnet to maximize overall performance.
-
The Right Atoms
Strong magnets begin with the right elemental composition. By carefully choosing precursors and adjusting the ratios of elements like iron, zinc, and strontium, the balance between the hard and soft magnetic phases could be tailored. This boosted the saturation magnetization which is the maximum possible strength of the magnet.
-
The Right Size
Magnetic properties depend strongly on the size of the nanoparticles. Too large, and the magnetic phases won’t couple well; too small, and performance drops. The chemical synthesis conditions were carefully optimized to achieve the correct sizes. This was complemented by computational studies that identified optimum size ranges for exchange-spring enhancement. Solid-state synthesis methods were also explored to transform nanocrystalline powders into bulk magnets. Careful control over thermal processing was key to achieving optimal nanoparticle size.
-
The Right Alignment
Even with perfect composition and size, the way particles are arranged also matters. Using TEM, XRF and XRD, Priyank analyzed how the magnetic phases were distributed and packed. Well-aligned, compact structures showed stronger magnetic coupling and better performance. Numerical simulations also confirmed that densely packed and highly aligned nanoparticles maximized magnetic performance.
Introducing AROS: Ultrafast Heating for Next-Gen Magnets
To improve control over the particle sizes and packing density in the final magnet, Priyank co-developed a custom setup for rapid, high-temperature synthesis: the Aarhus Rapid Ohmic Sintering (AROS) system. Traditional sintering processes can take hours and often damage sensitive nanostructures. With ramp rates of 9000 °C/min, AROS can easily heat samples up to 2500 °C within seconds. This rapid processing not only saves time and energy but also avoids the degradation seen in slower methods.
By combining ultrafast electrical Joule heating with real-time X-ray monitoring at synchrotron facilities in Germany (P02.1, PETRA-III) and Sweden (DanMAX, MAX IV), AROS enabled the observation of structural changes during sintering. These insights helped fine-tune the conditions to retain optimum nano-/microstructures which are critical for the magnetic performance.
In situ X-ray scattering experiments also confirmed that AROS could produce unique material phases that are not achievable through conventional heating, and on much shorter timescales. This opens entirely new pathways for laboratory and industrial scale production of permanent magnets.

Key findings
- Sol-gel routes need careful control to avoid unwanted reactions that could degrade magnet performance.
- Alternative chemical methods, like solvothermal synthesis, help produce purer, higher-performing ferrites.
- Combining solid-state synthesis with ultrafast heating unlocks faster and cleaner routes to functional magnets.
- Understanding structure at multiple length scales is vital to connect synthesis and processing steps to magnetic behavior.
Why Does It Matter?
This work supports the global push for viable magnets without rare earth elements. With advanced heating technology and a better grasp of synthesis-structure-property relationships, these ferrite-based magnets could help power next-generation green technologies at lower economic and environmental costs.
Interested? Read about it and stay tuned for more results from the Magnetic Matter group!
Priyank Shyam, Mathias Mørch, Anna Zink Eikeland, Jakob Ahlburg, Aref Mamakhel, Matilde Saura-Múzquiz and Mogens Christensen
[2] Optimizing the energy product of exchange-coupled soft/hard Zn0.2Fe2.8O4/SrFe12O19 magnets
Ofelia Traistaru, Priyank Shyam, Mogens Christensen and Søren Peder Madsen
[3] Sintering in seconds, elucidated by millisecond in situ diffraction
Priyank Shyam, Frederik H. Gjørup, Mathias Mørch, Amalie P. Laursen, Anna Z. Eikeland, Innokenty Kantor, Mads Ry Jørgensen and Mogens Christensen
[4] Aligned Permanent Magnet Made in Seconds–An In Situ Diffraction Study
Amalie P. Laursen, Jens P. Frandsen, Priyank Shyam, Mathias Mørch, Frederik H. Gjørup, Harikrishnan Vijayan, Mads Ry Jørgensen and Mogens Christensen
An updated version of the AROS sample environment is openly available for all users of the DanMAX beamline at MAX IV, Sweden.
If you are interested to know more about how ultrafast heating methods can help your research, you are welcome to contact Priyank Shyam, or the iMAT center manager to get you in touch with the right person.